Slikta ūdens izturība, nelīdzena virsma, augsts pulvera saturs un nevienmērīgs garums? Bieži sastopamas problēmas un uzlabošanas pasākumi ūdensdzīvnieku barības ražošanā
Mūsu ikdienas ūdens barības ražošanā esam saskārušies ar dažādām problēmām. Šeit ir daži piemēri, ko apspriest ar visiem:
1. Formula
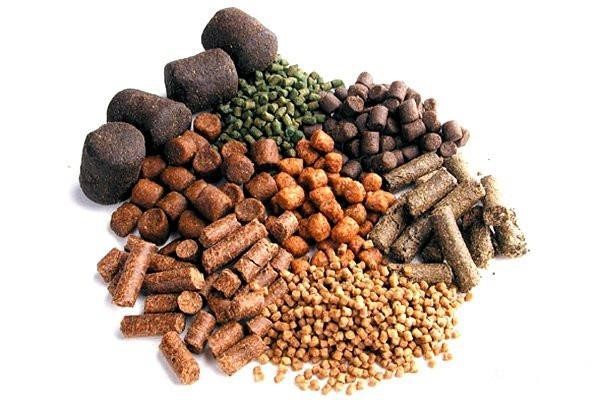
1. Zivju barības formulas struktūrā ir vairāki miltu izejvielu veidi, piemēram, rapšu milti, kokvilnas milti utt., kas pieder pie jēlšķiedras. Dažām eļļas rūpnīcām ir progresīvas tehnoloģijas, un eļļa būtībā tiek cepta sausā veidā ar ļoti mazu saturu. Turklāt šāda veida izejvielas ražošanā nav viegli absorbējamas, kas būtiski ietekmē granulāciju. Turklāt kokvilnas miltus ir grūti sasmalcināt, kas ietekmē efektivitāti.
2. Risinājums: Ir palielināta rapšu raušu izmantošana, un formulai ir pievienotas augstas kvalitātes vietējās sastāvdaļas, piemēram, rīsu klijas. Turklāt ir pievienoti kvieši, kas veido aptuveni 5–8% no formulas. Pielāgojot, granulācijas efekts 2009. gadā ir relatīvi ideāls, un ir palielinājusies arī raža no tonnas. 2,5 mm daļiņas ir no 8 līdz 9 tonnām, kas ir gandrīz par 2 tonnām vairāk nekā iepriekš. Arī daļiņu izskats ir ievērojami uzlabojies.
Turklāt, lai uzlabotu kokvilnas sēklu miltu sasmalcināšanas efektivitāti, pirms sasmalcināšanas mēs sajaucām kokvilnas sēklu miltus un rapšu sēklu miltus attiecībā 2:1. Pēc uzlabošanas sasmalcināšanas ātrums būtībā bija līdzvērtīgs rapšu sēklu miltu sasmalcināšanas ātrumam.
2. Nelīdzena daļiņu virsma
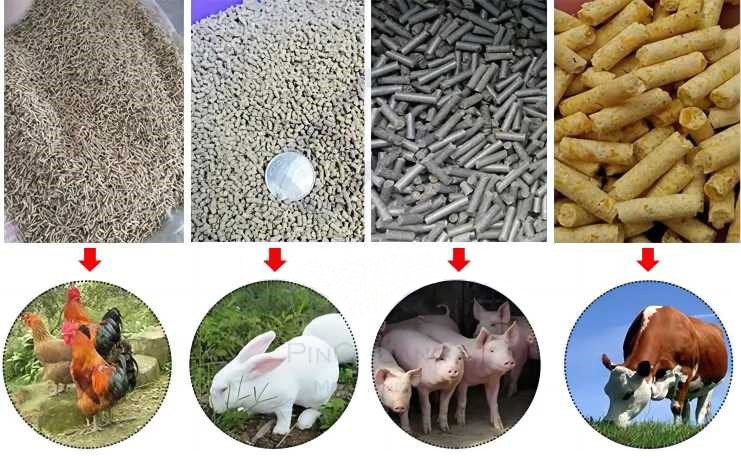
1. Tam ir liela ietekme uz gatavā produkta izskatu, un, pievienojot to ūdenim, tas ir pakļauts sabrukšanai un tam ir zems izmantošanas līmenis. Galvenais iemesls ir:
(1) Izejvielas tiek sasmalcinātas pārāk rupji, un rūdīšanas procesā tās nav pilnībā nogatavinātas un mīkstinātas, un, izlaižot caur veidņu caurumiem, tās nevar labi kombinēt ar citām izejvielām.
(2) Zivju barības formulā ar augstu jēlšķiedras saturu, izejvielā rūdīšanas procesā esošo tvaika burbuļu dēļ, šie burbuļi plīst spiediena starpības dēļ starp veidnes iekšpusi un ārpusi daļiņu saspiešanas laikā, kā rezultātā daļiņu virsma kļūst nevienmērīga.
2. Apstrādes pasākumi:
(1) Pareizi kontrolējiet saspiešanas procesu
Pašlaik, ražojot zivju barību, mūsu uzņēmums kā beramkravu izmanto 1,2 mm sieta mikropulveri. Mēs kontrolējam sieta lietošanas biežumu un āmura nodiluma pakāpi, lai nodrošinātu smalcināšanas smalkumu.
(2) Tvaika spiediena regulēšana
Saskaņā ar formulu ražošanas laikā tvaika spiedienu regulē saprātīgi, parasti kontrolējot aptuveni 0,2. Sakarā ar lielo rupjo šķiedru izejvielu daudzumu zivju barības formulā ir nepieciešams augstas kvalitātes tvaiks un saprātīgs atlaidināšanas laiks.
3. Slikta daļiņu ūdensizturība
1. Šāda veida problēma ir visizplatītākā mūsu ikdienas ražošanā, un tā parasti ir saistīta ar šādiem faktoriem:
(1) Īss atlaidināšanas laiks un zema atlaidināšanas temperatūra izraisa nevienmērīgu vai nepietiekamu atlaidināšanu, zemu nogatavošanās pakāpi un nepietiekamu mitruma līmeni.
(2) Nepietiekams līmvielu, piemēram, cietes, daudzums.
(3) Gredzena veidnes saspiešanas pakāpe ir pārāk zema.
(4) Formulā ir pārāk augsts eļļas saturs un jēlšķiedras izejvielu īpatsvars.
(5) Sasmalcināšanas daļiņu izmēra koeficients.
2. Apstrādes pasākumi:
(1) Uzlabojiet tvaika kvalitāti, noregulējiet regulatora lāpstiņas leņķi, pagariniet rūdīšanas laiku un atbilstoši palieliniet izejvielu mitruma saturu.
(2) Pielāgojiet formulu, attiecīgi palieliniet cietes izejvielu daudzumu un samaziniet tauku un jēlšķiedras izejvielu īpatsvaru.
(3) Ja nepieciešams, pievienojiet līmi. (Nātrija bāzes bentonīta suspensija)
(4) Uzlabot saspiešanas pakāpigredzena die
(5) Kontrolējiet saspiešanas smalkumu labi
4. Pārmērīgs pulvera saturs daļiņās
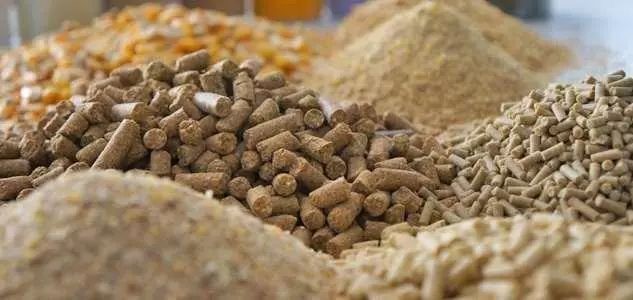
1. Pēc atdzesēšanas un pirms sijāšanas ir grūti nodrošināt vispārējas granulu barības izskatu. Klienti ir ziņojuši, ka granulās ir vairāk smalku pelnu un pulvera. Pamatojoties uz iepriekš minēto analīzi, es domāju, ka tam ir vairāki iemesli:
A. Daļiņu virsma nav gluda, griezums nav glīts, un daļiņas ir irdenas un pakļautas pulvera ražošanai;
B. Nepilnīga sijāšana ar šķirošanas sietu, aizsērējis sieta siets, nopietns gumijas bumbiņu nodilums, neatbilstoša sieta sieta atvere utt.;
C. Gatavās produkcijas noliktavā ir daudz smalku pelnu atlikumu, un klīrenss nav rūpīgs;
D. Iepakošanas un svēršanas laikā putekļu notīrīšanā pastāv slēptas briesmas;
Apstrādes pasākumi:
A. Optimizējiet formulas struktūru, saprātīgi izvēlieties gredzena veidni un labi kontrolējiet saspiešanas pakāpi.
B. Granulēšanas procesa laikā kontrolējiet atlaidināšanas laiku, padeves daudzumu un granulācijas temperatūru, lai izejvielas pilnībā nogatavotos un mīkstinātu.
C. Pārliecinieties, ka daļiņu šķērsgriezums ir glīts, un izmantojiet mīkstu griešanas nazi, kas izgatavots no tērauda sloksnes.
D. Pielāgojiet un uzturiet vērtēšanas ekrānu un izmantojiet saprātīgu ekrāna konfigurāciju.
E. Sekundārās sijāšanas tehnoloģijas izmantošana gatavās produkcijas noliktavā var ievērojami samazināt pulvera satura attiecību.
F. Gatavās produkcijas noliktava un ķēde ir jātīra savlaicīgi. Turklāt ir jāuzlabo iepakojums un putekļu noņemšanas ierīce. Putekļu noņemšanai vislabāk ir izmantot negatīvu spiedienu, kas ir ideālāk. Īpaši iepakošanas procesa laikā iepakošanas darbiniekam regulāri jāizsit un jātīra putekļi no iepakojuma svaru bufera tvertnes..
5. Daļiņu garums mainās
1. Ikdienas ražošanā mēs bieži sastopamies ar grūtībām kontrolē, īpaši modeļiem, kas pārsniedz 420. Iemesli tam ir aptuveni šādi:
(1) Granulācijas padeves daudzums ir nevienmērīgs, un atlaidināšanas efekts ievērojami svārstās.
(2) Nevienmērīga atstarpe starp veidnes veltņiem vai gredzenveida veidnes un spiediena veltņu smags nodilums.
(3) Gredzena veidnes aksiālajā virzienā izlādes ātrums abos galos ir mazāks nekā vidū.
(4) Gredzena veidnes spiedienu samazinošais caurums ir pārāk liels, un atvēršanas ātrums ir pārāk augsts.
(5) Griešanas asmens novietojums un leņķis ir nepamatoti nepareizi izvēlēts.
(6) Granulācijas temperatūra.
(7) Gredzenveida griešanas asmens tipam un efektīvajam augstumam (asmens platumam, platumam) ir ietekme.
(8) Tajā pašā laikā izejvielu sadalījums kompresijas kamerā ir nevienmērīgs.
2. Barības un granulu kvalitāte parasti tiek analizēta, pamatojoties uz to iekšējām un ārējām īpašībām. Kā ražošanas sistēma mēs esam vairāk pakļauti lietām, kas saistītas ar barības granulu ārējo kvalitāti. No ražošanas viedokļa faktorus, kas ietekmē ūdensdzīvnieku barības granulu kvalitāti, var aptuveni apkopot šādi:
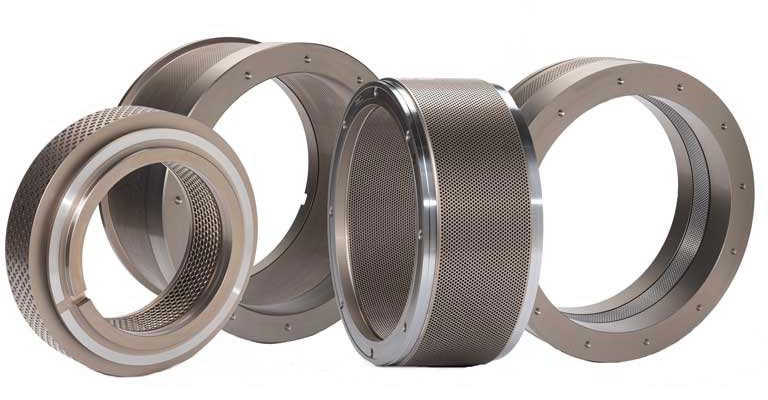
(1) Formulu izstrādei un organizācijai ir tieša ietekme uz ūdens barības granulu kvalitāti, veidojot aptuveni 40% no kopējā daudzuma;
(2) Saspiešanas intensitāte un daļiņu izmēra vienmērīgums;
(3) Gredzenveida veidnes diametrs, saspiešanas pakāpe un lineārais ātrums ietekmē daļiņu garumu un diametru;
(4) Gredzena veidnes saspiešanas pakāpe, lineārais ātrums, rūdīšanas un atlaidināšanas efekts, kā arī griešanas asmens ietekme uz daļiņu garumu;
(5) Izejvielu mitruma saturs, atlaidināšanas efekts, dzesēšana un žāvēšana ietekmē gatavo produktu mitruma saturu un izskatu;
(6) Pati iekārta, procesa faktori, kā arī dzēšanas un atlaidināšanas efekti ietekmē daļiņu pulvera saturu;
3. Apstrādes pasākumi:
(1) Pielāgojiet auduma skrāpja garumu, platumu un leņķi un nomainiet nodilušo skrāpi.
(2) Ražošanas sākumā un beigās pievērsiet uzmanību griešanas asmens pozīcijas savlaicīgai pielāgošanai nelielā padeves daudzuma dēļ.
(3) Ražošanas procesā jānodrošina stabils padeves ātrums un tvaika padeve. Ja tvaika spiediens ir zems un temperatūra nevar paaugstināties, tas savlaicīgi jāpielāgo vai jāaptur.
(4) Saprātīgi noregulējiet atstarpi starprullīša apvalksPēc jaunās veidnes ievietošanas uzstādiet jaunus veltņus un nekavējoties salabojiet spiediena veltņa un gredzena veidnes nelīdzenās virsmas, kas radušās nodiluma dēļ.
(5) Salabojiet gredzena veidnes vadotnes caurumu un nekavējoties notīriet aizsprostojušo veidnes caurumu.
(6) Pasūtot gredzena veidni, trīs caurumu rindu saspiešanas koeficients sākotnējās gredzena veidnes aksiālā virziena abos galos var būt par 1–2 mm mazāks nekā vidū.
(7) Izmantojiet mīkstu griešanas nazi ar biezumu no 0,5 līdz 1 mm, lai nodrošinātu pēc iespējas asu malu, lai tā atrastos uz gredzena veidnes un spiediena veltņa savienojuma līnijas.
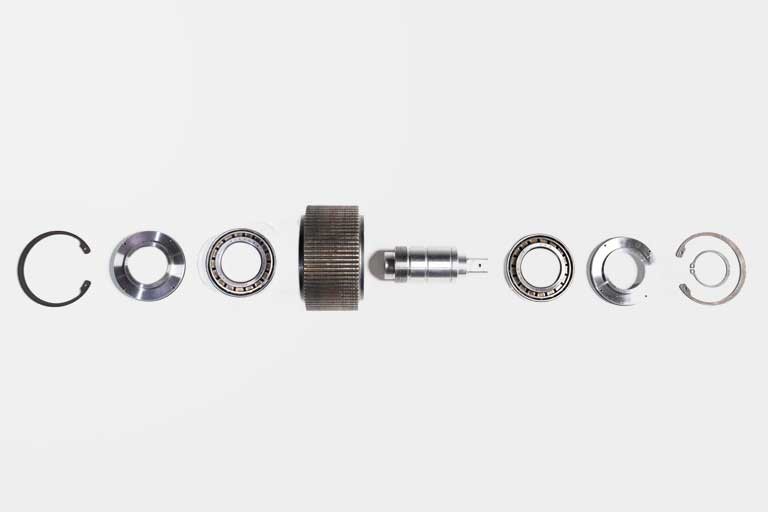
(8) Pārliecinieties par gredzenveida veidnes koncentriskumu, regulāri pārbaudiet granulatora vārpstas klīrensu un, ja nepieciešams, noregulējiet to.
6. Kopsavilkuma kontroles punkti:
1. Malšana: Malšanas smalkums jākontrolē atbilstoši specifikācijas prasībām
2. Sajaukšana: Izejvielu sajaukšanas vienmērīgums ir jākontrolē, lai nodrošinātu atbilstošu sajaukšanas daudzumu, sajaukšanas laiku, mitruma saturu un temperatūru.
3. Nogatavināšana: Jākontrolē uzpūšanas mašīnas spiediens, temperatūra un mitrums
Daļiņu materiāla izmērs un forma: jāizvēlas atbilstošas kompresijas veidņu un griešanas asmeņu specifikācijas.
5. Gatavās barības ūdens saturs: Ir jānodrošina žāvēšanas un dzesēšanas laiks un temperatūra.
6. Eļļas izsmidzināšana: Ir nepieciešams kontrolēt precīzu eļļas izsmidzināšanas daudzumu, sprauslu skaitu un eļļas kvalitāti.
7. Sijāšana: Izvēlieties sieta izmēru atbilstoši materiāla specifikācijām.
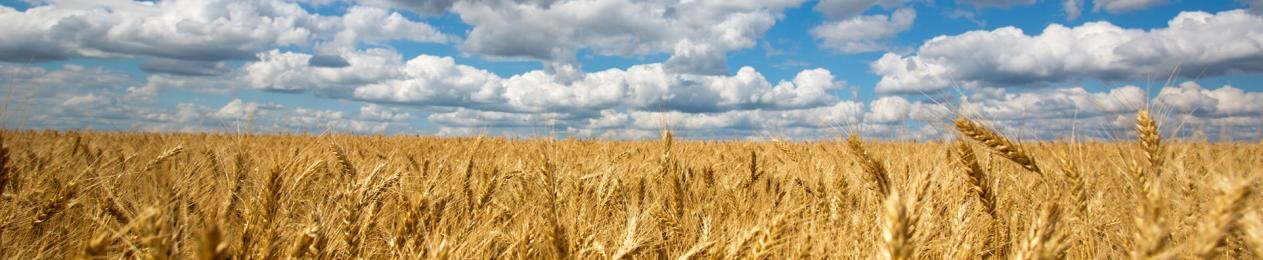
Publicēšanas laiks: 2023. gada 30. novembris